Aussie Infant Formula Manufacturer Automates End of Line Packaging Process to Keep up with Demand
- christinawindsor
- May 20, 2020
- 3 min read
Updated: Mar 30, 2022
Fibre King delivered a compact, affordable solution for a complex packaging line.

The Challenge: A popular Australian Infant Formula manufacturer wanted to increase the throughput of their production line which meant manual case packing and palletising were no longer going to be viable. They wanted a complete end of line solution which included case packing at up to 17 cases per minute and multiple formats, labelling, palletising, associated pallet handling and stretch wrapping. The solution needed to be cost effective as well as compact to be able to fit into their existing facility.
The Solution: Fibre King have supplied quite a number of case packing solutions for infant formula manufactures so were confident in their solution. The biggest challenge in this case was fitting the equipment into a very compact space while allowing access to operate the machines and bring in packaging consumables. The Engineering Applications team developed a customised solution to fit all the required equipment into the available space while not limiting functionality and production capacity. The solution was affordable, compact and flexible.
Services Rendered:
Bespoke design solution
Project management and seamless line integration of all equipment that included external suppliers
Full line simulation
Equipment Used:
Intermittent wrap around case packer fitted with cameras and software for serialisation requirements
Robotic Palletiser
ABB IRB460 Industrial Robot
Fromm Stretch wrapper
Infeed and outfeed Conveyors
Safety Fencing and Light Curtains
The Details: The final solution involved using a well proven intermittent wrap around case

packer with an offset inline infeed for collating the cans of formula. The client also had a requirement to run single serve pouches in cartons which required a secondary infeed to automatically collate the cartons for loading. The case packer also featured integrated cameras and software for serialisation integration. There were five different case configurations for the case packer to handle including three for cans and two for cartons.
Post case packing, a labeller integrated by Fibre King applies a label to the case which includes the serialised data from each can in the case. A camera system verifies the label data is correct and rejects cartons which cannot be verified prior to palletising. Rejected cartons are manually reworked and added back into the system.
The function of the Palletising System is to automatically dispense pallets, automatically dispense Pallet Board/Layer Pads, collate and palletise cases. The Palletising System includes the following components and facilities:
Infeed Conveyor from Case Packer
90 ° Case transfer including gapping hardware
Case Pick Off Conveyor
Pallet Board/Layer pad hopper
Fork Tyne Empty Pallet Dispenser
Palletising Turntable
Fromm Stretch wrapper
Full Pallet Outfeed Conveyor
ABB IRB460 Industrial Robot
Vacuum Gripper Head
Safety Fencing and Light Curtains

Pallet/Sheet handling
The operator places up to 10 empty pallets into the pallet dispenser. Once loaded, the pallet dispenser cycles leaving only the bottom pallet on the powered chain conveyor. The conveyor drives the empty pallet to a pallet turntable where it is aligned and is ready to receive cases. An operator manually loads the Pallet Board/Layer pads into the hopper, which holds up to 500mm of pads. Using the Vacuum gripper, the robot picks the top pad from the stack and place it onto the waiting pallet. The robot then loads the pallet with cases in the required pallet pattern and number of layers. Once a pallet is complete, it is driven from the loading turntable to the Stretch wrapper for wrapping. The pallet is completely wrapped and is driven out of the safety cell through a light curtain ready for pickup by forklift.
Case Handling
Cases travel one at a time out of the case packer and transfer onto a case conveyor and enter the robots’ safety zone. From here the cases index at 90° onto a case accumulation conveyor ready for pickup by the robots’ vacuum gripper. The gripper picks the cases from the pickup conveyor and places them onto the pallet in the desired pallet pattern until the pallet is complete.
A robot palletising system also incorporates serialisation and the ability to manually retrieve serial numbers if cases are rejected for any reason. The serialised data for the pallet is printed onto labels which are applied as per the Australian retail labelling standards (this labeller is supplied by others but integration has been supported by Fibre King).
Wrap up from James Windsor, CEO of Fibre King
“Having designed, built and installed infant formula end of line packaging solutions many times in the past made us the perfect fit for this popular Australian manufacturer. Even though the process is relatively similar across different projects we are consistently seeing an increase in demand for compact equipment that delivers flexible solutions. We are constantly adapting our equipment to meet the growing demands of production facilities and in doing so are seeing our equipment range evolve to incorporate smaller machines capable of more complex tasks, is quite exciting.”


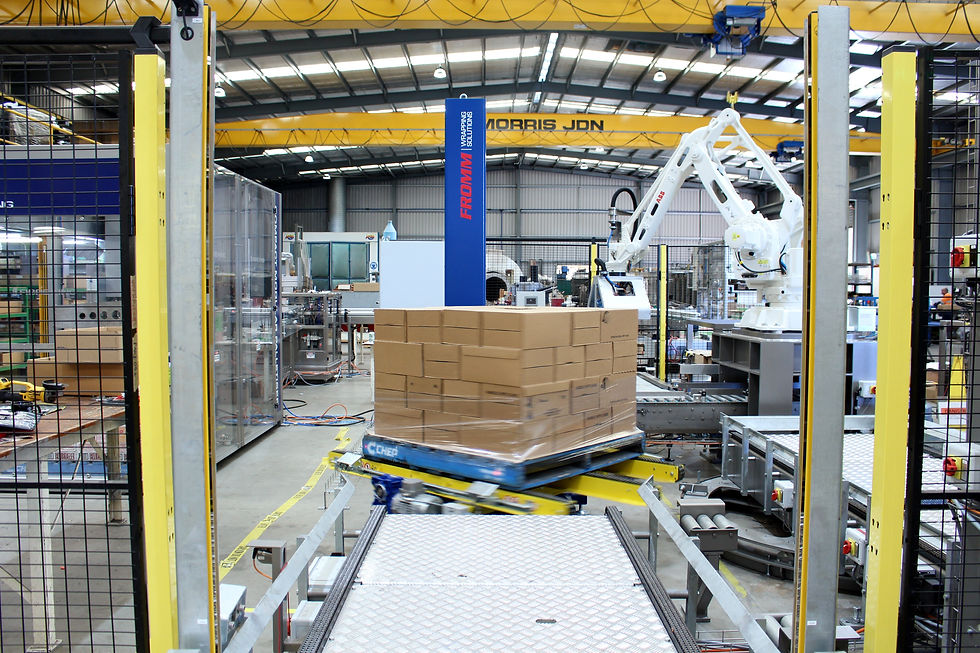


Comments